Ask Andrew: Understanding Fibreglass
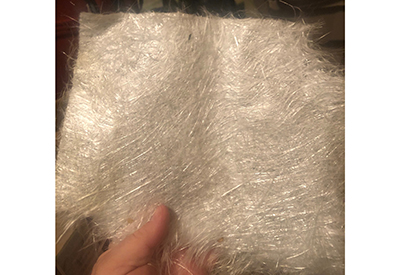
Mar 12, 2020
Last edition we talked about sealants to perform tasks like bedding and sealing. Other tasks like bonding, gluing, encapsulating and strengthening can be done using fiberglass, and the various resins available to saturate it.
A large portion of the boats on the water in Canada today are made using fiberglass – which is essentially a layer of fibrous stands, infused with a resin that will chemically react with a hardener, to make a strong, solid block. The way that the fibrous strands can be moved and molded, and the ways that resins can be strengthened have revolutionized boat building. As an extension of that, fiberglass care and construction are important to understand, so that repairs can be carried out.
Fibreglass is used in a number of ways aboard modern power and sailboats. It makes up the main hull shape, the bulkheads and stringers, the hatches and doors, the deck, coamings and cabin-top. The exterior is commonly a type of gelcoat that works (chemically) in a way that is similar to fiberglass. Modern boatbuilders are experimenting with carbon fibre and Kevlar to create deck hardware including cleats and winches.
Despite the marvels of engineering that fiberglass can perform, and it’s base it’s quite simple (once the chemistry is taken out):
Fibrous glass strands are infused with resin. The resin is a thick, syrup consistency that has had a chemical added to it that will react with the resin, causing it to change from a liquid to a solid. This solidifies around the layer of fibre, causing it to retain its shape, permanently, as a solid. Layers are added upon layers to the desired thickness of material.Layers can be bent, smoothed, molded and faired. The layers can be placed along a sandwiched layer of plywood, multiplying the strength, and effectively waterproofing the wood. The hardened fibres can be cut, shaped, smoothed and faired using common cutting and sanding tools.
fibreglass mat – a series of fibreglass strands pressed into a sheet. The sheet can be cut or torn apart to shape to fit.
The fibrous layer can come in many forms, namely: Woven mat (a pattern created by weaving, and the thickness of light wool), chopped mat (individual strands are compressed, creating a thick material, and cloth (a pattern created by weaving, but the thickness of cotton). Often, when creating a thick layer of fiberglass, these types of fibrous layers are alternated to provide strength and flexibility.
The resin alone can be thickened and strengthened, allowing it to be injected, puttied in place, or used as a fillet to strengthen a joint. Thickened resin is common in boat-yard repairs.
the left kit is a thickened epoxy – two tubes are included – one resin, one hardener – they are mixed in a 1:1 ratio. The bottle on the right is a polyester resin.
The resin can have a few different types of chemicals: Polyester, vinylester and epoxy. Polyester resins are quite common on modern sailboats. Vinylester is used in applications where a thinner liquid may be needed, but generally costs more that polyester.
Epoxies are the thickest of the three, and they harden in a different way. Epoxies are becoming more and more common, and marketed towards do-it-yourselfers in a variety of ways (pre-thickened, and in delivery through caulking gun or syringe). Epoxy also has the advantage of sticking to anything – chemically, it will bond with polyester and vinylester resins, but also to wood, aluminum, steel and a variety of marine coatings (paint and varnish).
Thickeners are used in a variety of ways: to allow the user to ‘putty’ the thickened resin into gaps, holes or voids, to strengthen the resin so that it can be used structurally, and to create a glue, to bond parts together. The thickeners chosen can thicken, strengthen and to make the resin sandable – these include microballoons, cabosil and talcum powder.
a bottle of MEKP – a catalyst/hardening agent for polyester and vinylester resins
The hardening agent for polyester and vinylester resins is a catalyst called MEKP and is added to the resin at a ratio of 1-2%. Epoxies utilize their own hardeners (each brand uses their own chemical formula).
Resins come in metal cans (like an once or gallon paint can), and are poured into a ‘mixing pot’, and the hardener and thickeners (if any) are then added and mixed. The fibrous layers are laid out in their desired form, and the hardened resin is added, and a spreader used to spread and saturate the fibrous layer. Layers are added to layers, each being saturated with resin as it’s laid up.
Resins can be purchased with or without wax additive, and can remain tacky unless another additive (Styrene or Air Dry) is mixed in.
Whenever resins are used, safety and efficiency are the name of the game. Resins are undergoing a chemical reaction, and are harmful in a few ways: skin contact, breathing the fumes, and eye exposure. Skin can be irritated via contact, and proper eye protection and respirators are necessary. Resins are also quite messy – so protect the work area (and yourself). Finally, the hardeners act chemically, and will cure fasted in heat (even the heat of your palm, holding the mixing pot can increase the speed of the reaction. Epoxies also generate quite a bit of heat (enough to melt a plastic or paper cup), so be careful of your choice of mixing pot!
Next edition, we’ll cover the uses and techniques that are used on common repairs, getting you ready to hit the ground running when spring hits!
Andrew McDonald is the owner of Lakeside Marine Services – a boat repair/maintenance firm based in Toronto. Andrew has worked in the marine industry for 12 years and is a graduate of the Georgian College ‘Mechanical Techniques – Marine Engine Mechanic’ program.
Questions or comments for Andrew? Email him directly via: askandrew@lakesidemarineservices.ca